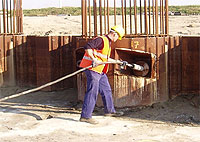
On construction drawings grout injection anchors are drawn as straight lines. Practice can be quite different: during the drilling process anchors can deviate easily from the intended path, both in the vertical and horizontal direction. There are good reasons why you would want to know the real shape of the anchor once it is in place.
To solve this measurement problem we developed ANCHORVIEW: an articulated chain of MEMS-chip multi-axial inclinometer segments that is lowered into the hollow core of the anchor. By subsequently reading-out all the segments in the chain the exact shape of the anchor is determined. As the measurement results are produced right on the spot in a matter of minutes ANCHORVIEW often is even used to verify the correct angle and shape during the drilling process itself. This technology is also used for soil freezing pipes, grout lines, boreholes and even things like prestressing ducts in concrete structures.
We carry-out these measurements as an independent party on a day rate basis.